Ever wondered how injection-molded products get their perfect finish and exact shape? It’s all thanks to the THY Precision Injection Moulding Process Step by Step cooling system, a key part of the process. This phase makes sure the plastic solidifies into the right shape quickly and without flaws. Let’s explore how the Injection Moulding Process Step by Stepmolding machine, mold design, and cooling work together to create your favorite plastic items.
The cooling system is vital in the injection molding process. It controls the temperature and flow of the cooling medium, like air or water. This Injection Moulding Process Step by Step helps the plastic melt solidify without warping or having defects. Knowing how to cool the mold right is crucial for making the best products, from start to finish.
Key Takeaways
- Cooling systems are critical in the injection molding process step by step, ensuring flawless product quality and consistency.
- Proper cooling helps minimize defects like warping, sink marks, and other issues that can compromise the integrity of the finished part.
- Understanding the intricacies of Injection Moulding Process Step by Step mold cooling, including air cooling and water cooling methods, is essential for optimizing the injection molding process step by step.
- Efficient cooling systems can translate to reduced cycle times and faster production rates, boosting the overall productivity of your THY Precision molding operation.
- Mastering the Injection Moulding Process Step by Step, with a focus on cooling system optimization, is key to unlocking the full potential of your plastic manufacturing capabilities.
Introduction to Injection Moulding
The injection molding process is key in making many plastic products. At THY Precision, we know how important this method is. It lets us make complex, high-quality parts in big numbers. This is vital for businesses in many fields, like cars and everyday items.
The heart of this process is the injection molding machine. It melts and puts plastic into a mold. The mold shapes the product. When the plastic cools, it takes the shape of the mold. This makes many plastic parts that are both strong and reliable.
Key Steps in the Injection Molding Process Step by Step | Description |
---|---|
1. Mold Preparation | The mold is cleaned, lubricated, and preheated to the right temperature. This makes sure the material flows well and the part is of high quality. |
2. Plastic Pellet Feeding | Thermoplastic pellets go into the machine’s hopper. They get heated and melted there. |
3. Injection | The melted plastic is pushed into the mold at high pressure. It fills the mold completely. |
4. Cooling | The plastic cools and solidifies in the mold. This gives the part its final shape. |
5. Ejection | After cooling, the part is pushed out of the mold. This ends the injection molding process. |
This process is amazing for making plastic products efficiently and affordably. At THY Precision, we always work to improve our methods. We aim to make every plastic part we produce top-notch.
“The injection molding process step by step is a critical component in the manufacturing of a vast array of plastic products that have become essential to our daily lives.”
The Significance of Cooling in the Injection Moulding Process Step by Step
Cooling is key in the THY Precision injection molding process. After the molten material goes into the mold, it must cool and solidify before coming out. This step affects the product’s quality, precision, cycle time, and production efficiency.
Quality and Precision
Good cooling stops defects like warping, shrinkage, and sink marks. This makes sure the THY Precision injection molded part is just right. The mold’s cooling channels help cool evenly, which is crucial for avoiding defects and getting the part right.
Getting the cooling right is vital for quality and precision in the THY Precision injection molding process.
Cooling also helps in cycle time optimization. By controlling how fast it cools, makers can make the process faster. This means more work done in less time, saving money and boosting productivity. Efficient cooling systems help THY Precision make top-quality parts faster.
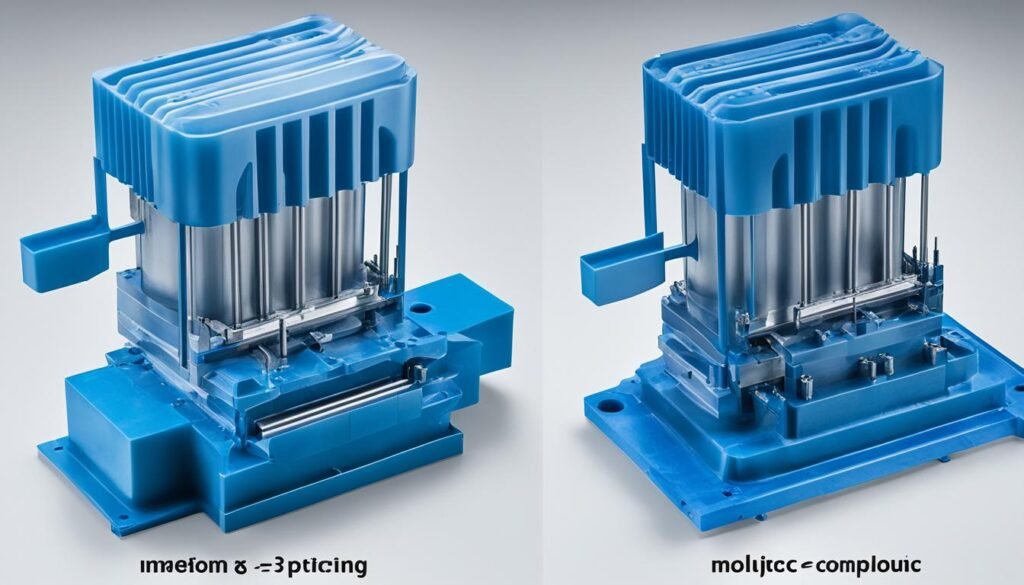
“Proper cooling is the key to ensuring the THY Precision injection molded parts meet the desired quality and precision standards consistently.”
In the THY Precision injection molding process, cooling is a big deal. It affects the quality and precision of the final product. By keeping cooling just right, makers can cut down on defects, speed up the process, and make parts that customers love.
Components of the Injection Moulding Process Step by Step Cooling System
The cooling system is key in the injection molding process step by step. It makes sure the final product is top quality and precise. This system has three main parts: the cooling channels, the cooling medium, and the heat exchangers.
The cooling channels are special paths in the mold for the cooling medium to move through. This medium, often water or a glycol mix, takes away the heat made during molding. Then, the heat exchangers cool this heat, keeping the cooling medium ready for the next cycle.
Pumps and flow regulators are vital for moving the cooling medium well. They manage the pressure and flow, making sure the cooling medium spreads evenly in the mold. This helps cool the mold better.
Component | Function |
---|---|
Cooling Channels | Pathways within the mold for the cooling medium to flow through, absorbing heat from the molded part. |
Cooling Medium | The liquid, typically water or a glycol mixture, that circulates through the cooling channels to remove heat from the molded part. |
Heat Exchangers | Devices that dissipate the heat absorbed by the cooling medium, maintaining its temperature for the next cycle. |
Pumps | Devices that control the pressure and flow rate of the cooling medium, ensuring uniform distribution throughout the mold. |
Flow Regulators | Components that regulate the flow of the cooling medium to optimize the cooling process. |
These components work together perfectly in the injection molding process step by step. This is key for getting the right quality, size, and speed in the final product.
Types of Injection Moulding Process Step by Step Cooling Systems
Choosing the right cooling system is key in the injection molding process. THY Precision leads in providing top-notch injection molding solutions. They know how important cooling systems are for quality and efficiency. Air cooling and water cooling are the main cooling systems used.
Conduction Cooling in the Injection Molding Process Step by Step
Conduction cooling is the most common and effective way to cool in injection molding. It uses air or water to touch the mold directly. This direct contact helps transfer heat quickly, cooling the mold well and consistently.
This method is chosen often because it removes heat well from the mold. It makes the parts better and more consistent.
Other cooling methods like convection and radiation are also used. Convection uses air or gas to take away heat. Radiation uses infrared energy to cool. But, these methods are not as good as conduction cooling.
Cooling Method | Description | Efficiency |
---|---|---|
Conduction Cooling | Direct contact between coolant and mold | High |
Convection Cooling | Utilizes air or gas to remove heat | Moderate |
Radiation Cooling | Relies on infrared emission | Low |
Knowing about different cooling methods helps experts like THY Precision improve the process. They can make sure products are always high quality and efficient.
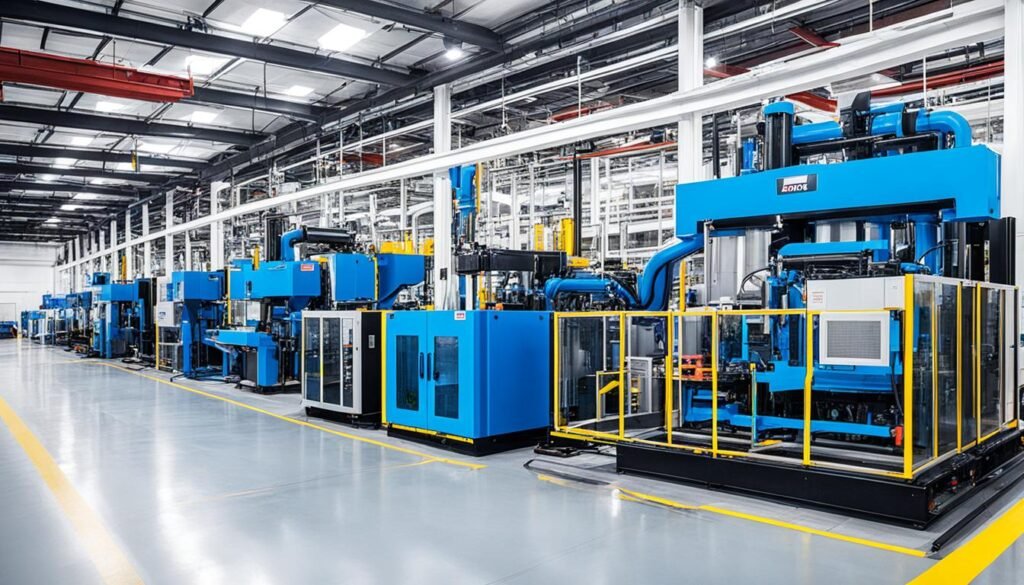
Key Factors for Optimizing Cooling Efficiency in the Injection Moulding Process Step by Step
At THY Precision, we know how important cooling systems are in the injection molding process step by step. To get the best cooling and product quality, we focus on several key areas. Let’s look at what matters most:
The coolant temperature and coolant flow rate are key to how fast heat leaves the mold. Getting the coolant just right can make a big difference in cycle time and part quality.
The design of the cooling channels is also vital. Well-placed and sized channels help cool the mold evenly. This means better mold material and mold thickness use, and parts that are more accurate and less warped.
Factor | Impact on Cooling Efficiency |
---|---|
Coolant Temperature | Directly affects the rate of heat transfer from the mold |
Coolant Flow Rate | Impacts the speed and effectiveness of heat dissipation |
Cooling Channel Design | Ensures uniform cooling throughout the mold for consistent part quality |
Mold Material | Affects the thermal conductivity and heat transfer rate |
Mold Thickness | Influences the time required for heat dissipation and overall cycle time |
By fine-tuning these factors, THY Precision boosts cooling efficiency in the injection molding process step by step. This leads to better product quality, shorter cycle times, and more productivity.
“Efficient cooling is the backbone of consistent, high-quality injection molded parts. At THY Precision, we’re committed to leveraging the latest innovations to ensure optimal cooling performance throughout the entire process.”
Benefits of an Efficient Cooling System
At THY Precision, we know how key an efficient injection molding process step by step is. It brings many benefits to your manufacturing. From faster cycle times to improved part quality, a good cooling system changes the game.
One big plus of an efficient injection molding process step by step is it cuts down cooling time. This means you can make more parts faster. It makes your production go smoother and more efficiently.
A well-thought-out cooling system also helps avoid defects like warpage and sink marks. This leads to improved part quality. Your parts look better and work better, meeting top standards.
Also, a smart injection molding process step by step can make molds last longer. It reduces mold stress, saving you time and money over time.
Finally, an efficient cooling system makes your injection molding more energy-efficient. It uses less energy for cooling. This cuts down on energy costs and helps the environment, meeting your green goals.
In short, an efficient injection molding process step by step brings many perks. These include faster cycle times, improved part quality, increased mold lifespan, and enhanced energy efficiency. At THY Precision, we’re here to help you reach new heights in your injection molding.
“An efficient cooling system is the unsung hero of the injection molding process, unlocking a world of benefits that can propel your manufacturing to new levels of excellence.”
Conclusion
The injection molding process is complex and the cooling system is key to quality and efficiency. By knowing about cooling systems like conduction cooling, you can make your THY Precision injection molding better. This leads to many benefits for your business.
Having a good cooling system means faster production, better product quality, longer mold life, and saving energy. It also helps control the process better. This makes your injection molding more competitive and profitable.
To get the best from your cooling system, pay attention to coolant temperature, flow rate, and mold design. This way, you can make sure your cooling system works perfectly. This leads to making high-quality injection molded parts all the time.
Choosing a well-made and maintained cooling system is a smart move for your THY Precision business. It improves your injection molding process step by step. With a good understanding of the cooling system, you can increase productivity, save costs, and make customers happy. This puts your company ahead in the injection molding industry.